Things You'll Need
Nonflammable worktable
Roll of emery cloth
Silver solder flux
Acid brush
Safety glasses
Leather work gloves
Oxy-acetylene torch
Striker
Silver solder
Lineman's pliers
Water-filled bucket
Clean rag
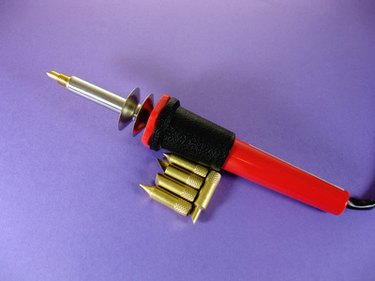
Silver soldering, also known as hard soldering or silver brazing, uses a silver-based solder to join two or more pieces of dissimilar metal. The process of silvering soldering is not the same process you may be used to performing on copper piping or electrical wiring. Melting temperatures for silver solder range from 1240 to 1365 degrees F, four imes higher than tin solder's average of 345 degrees Ft. This drastic heat requirement changes the type of torch needed for silver soldering and the way a silver solder joint fits together.
Step 1
Place the two dissimilar pieces of metal on the nonflammable worktable.
Video of the Day
Step 2
Tear 3 inches of material from the roll of emery cloth, and clean the sides of both pieces of metal to a silvery shine.
Step 3
Align the pieces of metal. This will be the joined position of the metal pieces after soldering. Make sure you position the pieces properly.
Step 4
Apply silver solder flux to the area where the pieces of metal meet with the acid brush. Do not use standard low-temperature flux, as it will burn, contaminating the solder joint and compromising the flow of the silver solder.
Step 5
Don your safety glasses and leather work gloves.
Step 6
Light the oxy-acetylene torch with the striker, and heat the entire length of the fluxed solder joint.
Step 7
Rub the silver solder onto the heated joint. When the solder melts quickly and flows immediately into the solder joint, run the silver solder along the entire joint between the metals.
Step 8
Turn off the oxy-acetylene torch, pick up the silver soldered metals with the lineman's pliers, and drop the joined metals into the water-filled bucket. Allow the pieces to cool for 30 to 60 seconds before removing the metal pieces from the water.
Step 9
Dry the cooled pieces of metal with a clean rag.
Video of the Day