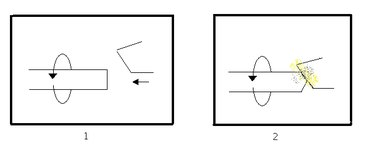
Making the Tip
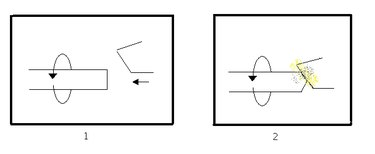
A drill bit starts as a rod made from a durable steel alloy. The rod is cylindrical with flat ends and usually has the same diameter as when the drill bit is completely finished. First, one of the flat ends must be transformed into a gently-sloping, cone-shaped tip. To accomplish this, a fully-automated machine grasps the rod and rotates it rapidly (i.e. over 1,000 revolutions per minute) about its axis (Figure 1). Meanwhile, the machine lowers a special stationary blade so that it touches the edge of the rod at an angle. The spinning of the rod grinds the entire circumference of the edge into the blade, gradually wearing it down until only a cone remains.
Cutting the Flutes
Video of the Day
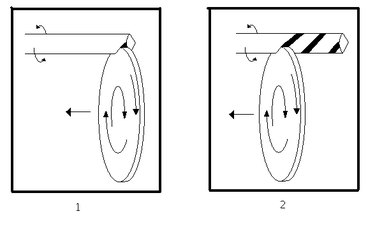
The machine stops spinning the rod and moves it into position for cutting the flutes. Here, a thin circular saw (usually made from ceramics, artificial diamond or other heavy-duty composite) angled diagonally to the rod cuts less than a millimeter into the side. As this happens, the saw slowly moves parallel to the rod as the machine slowly rotates the rod, resulting in a smooth helical groove (a.k.a. the "flute") along the length (Figure 2). Once the saw reaches the end of the drill bit, the machine repositions the saw at the front to cut the second flute into the rod.
Video of the Day
Titanium Coating
To make the drill bit more durable, the manufacturer adds a thin coat of titanium nitride (TiN) to the entire surface. Titanium nitride is most commonly applied through a process called "physical vapor deposition" (PVD). In PVD, the drill bit is placed in a vacuum-sealed chamber with solid titanium nitride situated adjacently. When titanium nitride is heated in a very low-pressure environment (i.e. a vacuum), it "sublimates": turning directly from a solid into a gas.
Meanwhile, this gas slowly deposits on the surface of the drill one molecule at a time, until the entire body is covered in a thin, durable film.