Things You'll Need
Angle grinder
Scrap steel
Steel clamps
Welder
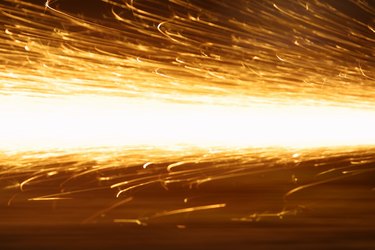
H-Beams -- also called I-Beams or girders -- are more expensive and more difficult to transport in longer lengths. You can weld to H-beams together, end-to-end, to avoid the difficulties of shipping a 50-foot beam, for example. A good weld will provide as much or more strength as non-welded segments beam. The ability to weld beams in the field, also provides greater flexibility in your materials planning and management.
Step 1
Bevel the edges of the H-beams' ends where they will be joined. The bevel on each beam, as they are brought together, will form a V-shape which will facilitate good penetration; the arc will penetrate the metal, which coalesces easier in the V, rather than lapping one layer of metal over another. Use an angle grinder to bevel each edge on the entire perimeter of each end.
Video of the Day
Step 2
Align the H-beams end-to-end. Make sure they are properly aligned.
Step 3
Clamp the two beams together. With two heavy pieces of steel such as H-beams, gravity may hold them in position for you. You need to clamp, at very least, so your welder can be ground to not one, but both pieces. Use scrap steel and steel clamps that span both pieces.
Step 4
Tack weld the ends together at each of the outside corners of the H-beam. You can use a MIG or metal inert gas welder, or a stick welder.
Step 5
Run a welded bead in the V-groove created by the bevels, starting at your first tack weld. Rather than welding continuously around the entire perimeter, break it up into sections to avoid warping the beam from concentrated heat. Weld half the top, then half the bottom, on the opposite corner. Weld half the side, then half the other side on the opposite corner. Keep alternating for heat management until the entire perimeter has been welded.
Warning
Most welding takes years of training to master. Structural steel members, require significant training and inspection by a building inspection to be used in a building.
Video of the Day