Things You'll Need
Heat-treat oven or forge
Leather gloves
Safety glasses
Tongs
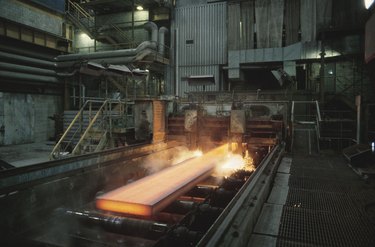
American Iron and Steel Institute-grade D2 tool steel is a high-alloy, high-carbon steel developed for additional strength and toughness. The steel has a high chromium content (11 to 13 percent) and relatively high amounts of molybdenum (.7 to 1.2 percent), vanadium (1.1 percent), cobalt (1 percent) and other elements. This complex mixture makes proper heat treatment of AISI D2 more complex than the heat treatment of other simple and tool steels.
Step 1
Preheat the steel by slowly raising the temperature to between 750 and 780 degrees Celsius. The rise in temperature should be accomplished over 45 minutes and up to two hours, depending on the mass of the steel. Larger pieces of steel will require a longer preheat period than smaller pieces. This prepares the steel for further heating and prevents unnecessary stress from forming in the steel.
Video of the Day
Step 2
Raise the temperature to between 1,000 and 1,030 degrees Celsius and allow the steel to soak thoroughly to ensure the steel is heated though. Typically, a soak time of between 45 minutes and 1 hour is sufficient. However, very large sections of steel, or those weighing more than 50 pounds, require longer soak times -- sometimes in excess of 12 hours -- and are best suited for industrial heat treating processes.
Step 3
Remove the steel from the oven and allow it to cool to room temperature. This is the final step prior to tempering.
Step 4
Temper the steel by raising the temperature to 150 degrees Celsius and allowing the steel to cool. This will result in a hardness of approximately 62 Rockwell hardness.
Tip
Longer soak times are required for thicker pieces of steel. Massive sections may respond poorly to air cooling and may require a quench in preheated oil.
Warning
Heat-treating steel requires extreme heat, so proper safety equipment and procedures must be used to prevent serious injury.
Video of the Day