Things You'll Need
Potter's wheel
Porcelain clay
Kiln
Potters' glaze
Water
Elephant ear sponge
Wood, metal, or carbide modeling tools
Pencils
Curved wood ceramicist's rib
Straight wood ceramicist's rib
Needle tools
Cutting wire/string
Ceramic stands
Plaster bat
Pyrometric cones for porcelain and glazes
Prop or silica sand
Paint brushes in various sizes
2 to 3 buckets
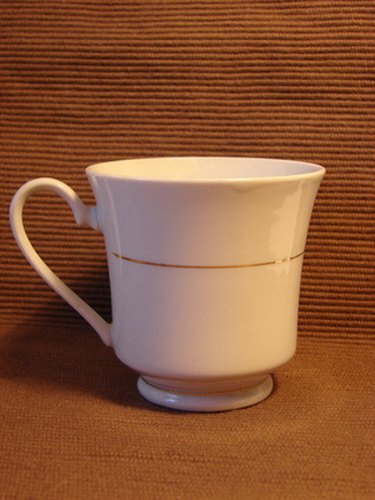
Throwing–the act of making ceramics on a potter's wheel–is a fun and often relaxing hobby for beginning and experienced potters alike. Beyond creating works of art, making pottery such as porcelain ceramic tea cups also allows the potter to make functional pieces that can be used daily. Working with porcelain, however, takes time and a great deal of skill.
Prepare Porcelain Clay
Step 1
On a flat surface, knead and wedge clay to remove air pockets.
Video of the Day
Step 2
Separate a small portion of porcelain for the handle and set aside in airtight, plastic bag to keep from drying out.
Step 3
Place a small piece of wet stoneware or earthenware clay on the center of the wheel and affix plaster bat.
Throwing the Porcelain
Step 1
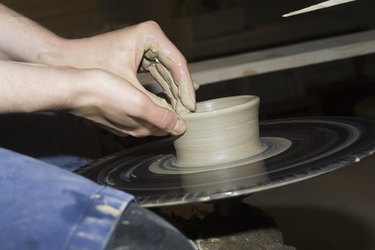
Firmly place the large piece of wedged porcelain onto the bat. (Also called centering the clay.) Place your least dominant hand with the palm alongside the porcelain mound and with the pinky-side on the wheel.
Step 2
Place your dominant hand just above the mound, palm facing down, and your fingers pointing towards the wheel. Leave your thumb free.
Step 3
Start the wheel using the foot pedals)Working the porcelain with both hands, apply pressure to the sides and tops, pulling the porcelain up and down until you have a cylinder. Add porcelain slurry sparingly as necessary to keep the porcelain moist as you work it.
Step 4
Insert the thumb of your dominant hand into the center of the porcelain to make a hole. Use your fingers to pull up the porcelain open for the body of the cup. Keep working the porcelain until you have your desired tea cup shape. Remember to add porcelain slurry sparingly as necessary to keep the porcelain moist as you work it.
Step 5
While the cup is still on the wheel, use modeling tools to remove areas of porcelain 1/4 inch from the wheel. Reduce wheel speed, while maintaining the form of the cup with your hands until the wheel stops.
Shaping the Handle
Step 1
When the wheel has stopped, remove the cup from the wheel with the wire, scraping it along the wheel to ensure complete removal. Take the cup body to your main working surface.
Step 2
Remove set-aside porcelain from bag and shape into a handle.
Step 3
Wet the ends of the handle with porcelain slurry and where they will attach to the body of the cup. Attach the handle to the cup, smoothing out the seams where the handle and cup meet. Adjust shape and angle of the handle as necessary.
Step 4
Let the cup dry in an airtight container. (Cup may need to dry overnight.) Before cup hardens completely, you can trim, carve lightly, sponge, sand lightly and make other pre-firing finishing touches to make the porcelain as smooth as possible.
Step 5
Repeat all previous steps for additional cups.
Baking the Porcelain
Step 1
When all cups are completely dry and no longer maleable, place cups in the kiln on prop or silica sand. Be sure to space evenly to avoid having the cups touch.
Step 2
"Bake" according to the pyrometric cone that you are using for your porcelain. For bisque firing, you bake the porcelain at around 1900 degrees Farenheit (1038 degrees Celsius). For "China" firing, bake at temperatures ranging between 2345 to 2462 degrees Farenheit (1285-1350 degrees Celsius).
Step 3
Remove cups from kiln and allow to cool for a day.
Step 4
When fired cups are cool, rinse each in a water bath to remove dust.
Glazing and Finishing
Step 1
When bathed cups are dry, glaze according to glaze manufacturer's directions by painting with brushes or dipping in a glaze bath.
Step 2
"Bake" glazed cups in kiln according to glaze manufacturer's recommendations and according to the pyrometric cones that you are using for that glaze.
Step 3
When glaze is set, remove from kiln and let cool. Repeat glazing process if desired.
Tip
Use glaze that is food-safe if the cups will be used for drinking.
You may need several different pyrometric cones–some appropriate for your porcelain and some appropriate for your glazes.
Practice your tea cup shape with other clay before working with the porcelain.
Always use mitts and other protective gear when removing items from the kiln.
Add designs to the cup before glazing with clear ceramic glaze.
Consider dipping the foot, rim or handles in a different pigment color before the final clear glaze.
Warning
Porcelain has "memory," so be sure to make all surfaces as smooth as possible.
To ensure best glaze adhesion, make sure fired pot is free from dust and debris, including oils and dirt from hands.
Allow pot to dry completely before glazing.
To avoid distortion, do not overfire. Pay close attention to the pyrometric cones.
Make sure brushes and dipping vessels are clean to avoid defects in the glaze.
Video of the Day