Things You'll Need
Sandpaper
Fitting brush
Soldering flux
Brass sweat adapter coupling
Propane torch
Solder
Hose clamp
Screwdriver
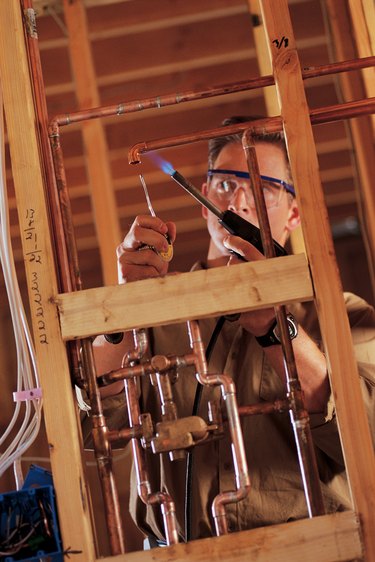
Copper pipe is very durable, resists corrosion and is commonly used for a variety of piping applications including water piping, compressed air piping, drain piping and refrigeration piping. However, copper piping is tedious to install because each turn or bend requires a fitting soldered on. This can become very time-consuming. Polyethylene tubing is flexible and can twist and turn easily. If you have an application where you need to make lots of turns, you can connect your copper pipe to polyethylene tubing to finish the installation.
Step 1
Clean the end of the copper pipe with sandpaper until it is smooth and shiny. This removes dirt, grease and other debris to allow solder to stick.
Video of the Day
Step 2
Brush the inside of the brass sweat adapter coupling with your fitting brush.
Step 3
Brush soldering flux on the outside of the copper pipe end and to the inside of the brass sweat adapter coupling. Slide the coupling onto the copper pipe.
Step 4
Heat the brass fitting with a propane torch. Unroll your solder and place the end on the joint between the coupling and the pipe. Allow the torch to heat the fitting until the solder melts. Quickly drag the solder around the joint and remove the torch.
Step 5
Allow the fitting to cool until it is cool to the touch. Slide a hose clamp over one end of your polyethylene tubing and push the tubing onto the barbed end of the brass sweat adapter coupling.
Step 6
Slide the hose clamp back toward the end of the tubing until it is over the barbed end of the adapter coupling. Tighten with a screwdriver until it is clamping the hose tightly to the adapter coupling.
Warning
Do not slide the polyethylene tubing onto the adapter coupling until it is sufficiently cool. Doing so while it is hot will cause the tubing to melt or even catch fire.
Video of the Day