Things You'll Need
Calipers
Ruler
Calculator
MIG wire
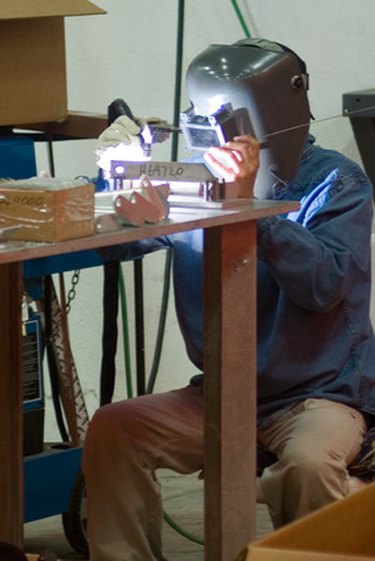
Metal inert gas (MIG) welding machines automatically feed wire through the torch head of the welding gun to the weld site. This wire acts both as the electrode that arcs with the metal being welded to create the weld bead and as filler material to join the metal pieces. To ensure a proper joint is created, the MIG wire must be fed to the weld at an appropriate speed.
Step 1
Measure the thickness of the metals you are joining together using calipers and a ruler.
Video of the Day
Step 2
Convert the standard measurement into decimals by dividing the numerator by the denominator. For example, if your plate is 1/8 inch thick, divide 1 by 8 to get 0.125 inch.
Step 3
Convert your measurement into amperes. Each 100th of an inch of metal requires one ampere. Therefore, 1/8 inch thick metal requires 125 amps to properly weld the joint.
Step 4
Identify the diameter of the MIG wire that you will be using for your weld. The wire manufacturer lists a wire burn rate in inches per ampere on the packaging. For example, the 0.030 gauge wire required of 125 amp welding has a burn rate of 2 inches of wire per 125 amps.
Step 5
Multiply the required amperage of your weld by the burn rate associated with the diameter of the wire to calculate the feed speed. Using our example, you would multiply the 125 amps by the 2 inch burn rate to calculate a feed speed of 250 inches per minute.
Warning
Always refer to the manufacturer's instructions when learning to operate new equipment.
Video of the Day