Things You'll Need
Soapy water
Wrench
Teflon tape
Angle grinder
Brazing torch
Brazing rod
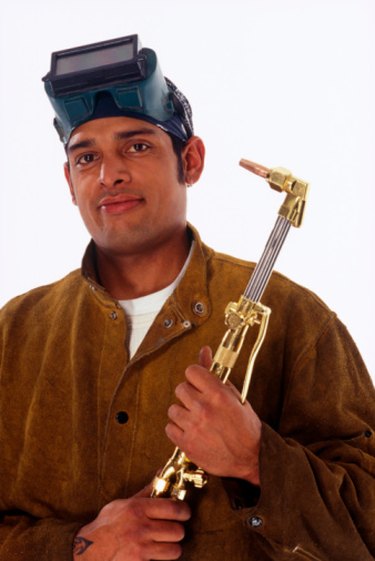
A compressor that won't charge, or won't hold pressure, is troublesome, at least. When that occurs, be sure to follow a troubleshooting guide to eliminate other possible causes, such as condensation in the tank and leaky tools, before assuming you have a leak in the tank. Most leaks will occur due to loose or incorrectly installed fittings. If you find that the leak is in the tank but is not on a seam or welded joint, the tank has been weakened to the point it should be replaced, rather than repaired.
Step 1
Disconnect all hoses and tools. Turn the compressor on and allow it to charge fully. Use a spray bottle of soapy water to spray around fittings, including the emergency release valve and tank-bleed fitting on the bottom of the tank. Look for bubbles to indicate escaping air. Use a wrench to tighten fittings that have air escaping. If bubbling persists, continue to the next step.
Video of the Day
Step 2
Pull the ring on the emergency release valve to release the pressure from the tank. Use a wrench to remove fittings that showed signs of leaking. Turn them counterclockwise to loosen and remove. Replace fittings that appear worn or damaged. Wrap Teflon tape around the threads and insert the new fitting, turning it clockwise to tighten it. Recharge the compressor and spray with soapy water to test again.
Step 3
Spray the tank with the soap solution if the leaking persists and is not related to fittings. Look for bubbling around welded-on brackets and at the seams of the tank. Mark areas that appear to be leaking with chalk.
Step 4
Turn the power off to the compressor, or unplug the power cord. Release the pressure from the tank with the release valve as before. Use an angle grinder to grind off the raised metal at the weld or seam to expose the hole or crack. Grind the surface until it flush and smooth with the surface of the tank.
Step 5
Light a brazing torch. Turn on the gas and use a welding lighter to spark the torch to life. Turn on the oxygen until the flame is bright blue, and heat the area to be repaired. Use a brass brazing rod to rebuild the welded area and seal the tank. Press the heated rod to the metal until it melts and pools, keeping the torch on the metal as it melts, covering the damaged area. Allow the repair to cool completely before turning the compressor back on and allowing it to recharge.
Warning
Under no circumstances should a badly damaged, or rusted tank be patched, welded or brazed. The risk of explosion is too high to risk patching anything other than a broken weld, or weak seam.
Video of the Day