Things You'll Need
Heat treat oven or forge
Quenching vessel
Mineral oil
Gloves
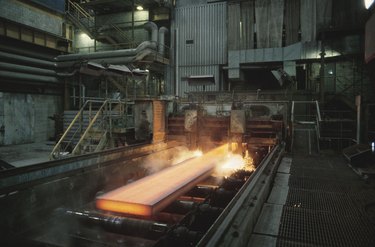
American Iron and Steel Institute grade 1095 steel is a high carbon, simple steel. Chemically, the steel contains just carbon, .90 to 1.04 percent, manganese, .30 to .50 percent, phosphorus, .020 percent maximum, sulfur, .025 max, and silicon, .15 to .30 percent. It is the highest carbon simple steel available and must be heat treated to be properly hardened. The heat treatment process involves normalizing, quenching and tempering, and results in a specific hardness depending on temperatures used.
Heating and Cooling
Step 1
Place the steel into a heat treat oven or forge and raise the temperature to between 1,550 degrees Fahrenheit and 1,650 degrees Fahrenheit. Allow the steel to remain in the oven for a "soak" time of at least 30 minutes. Allow more soak time for more massive pieces of steel.
Video of the Day
Step 2
Remove the steel from the oven and immediately quench by submerging the steel in oil until the temperature drops below 250 degrees Fahrenheit. Once quenched, allow the steel to cool to room temperature.
Step 3
Place the steel back in the oven and bring the steel up to tempering temperature. The tempering temperature correlates to the final desired hardness. A 400 degree Fahrenheit temper will result in a Rockwell hardness of 62; 600 degrees Fahrenheit results in RC 55; 700 degrees Fahrenheit results in RC 49 800 degrees Fahrenheit results in RC 45. Higher tempering temperatures lowers the resulting hardness. Once the steel reaches the appropriate temperature, remove the steel and allow to cool to room temperature.
Tip
A heat treat furnace allow precise temperature control. If capable, a home oven can be used for lower tempering temperatures.
Warning
Temperatures used in heat treatment can cause extreme burns. Proper safety equipment and procedures should be followed to prevent serious burns.
Video of the Day