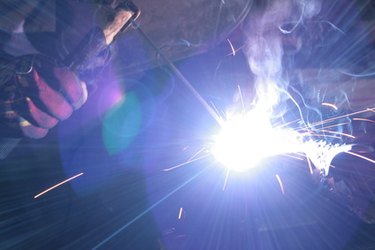
Arc welding was first demonstrated in 1881 by Nikolai Benardos, a Russian inventor. He used a carbon rod as an electrode and a metal rod as filler metal. It was made more practical in 1904 when a Swede, Oscar Kjellberg, invented the covered electrode. There are several different kinds of arc welding, including metal inert gas (MIG) and tungsten inert gas (TIG) welding. For the purposes of this article, we will consider a common arc welding technique, shielded metal arc welding, for comparison with MIG and TIG welding.
Shielded Metal Arc Welding
Video of the Day
Shielded metal arc welding is also called stick welding. Like all arc welding techniques, it uses electric current to create an electrical arc between the metal and the electrode. The arc provides the necessary heat to melt the metal, and the electrode provides filler metal and flux. In the case of shielded metal arc welding, the electrode is coated in flux, which not only helps create the arc, but also covers the weld puddle with shielding gas and slag to prevent atmospheric contamination.
Video of the Day
MIG Welding
MIG welding is more properly, but more infrequently called gas metal arc welding (GMAW), because the shielding gas is not always an inert gas. A spool of steel wire is machine-fed to the contact tip of the MIG gun, and the metal and wire are melted to form the weld puddle. The shielding gas, usually argon, is fed through the MIG gun. MIG welding is more efficient than shielded arc welding, and because of fewer stops and starts, it can produce a higher quality weld. It also lends itself well to robotic welding.
TIG Welding
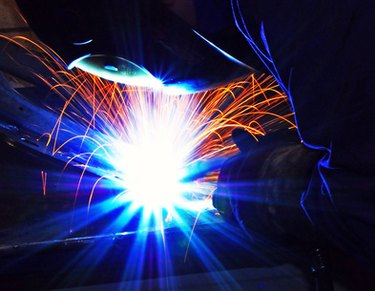
Just as with MIG welding and for the same reason, the more proper name for TIG welding is gas tungsten arc welding (GTAW). TIG welding uses non-combustible tungsten as an electrode, and the weld puddle is formed from the melted base metal. Any fill metal is added to the puddle using a separate filler wire or rod. The shielding gas is provided via a ceramic nozzle on the gun. TIG welds are still higher quality than MIG, and because the weld in made primarily of the target metals, it can be used for a wider range of metals and alloys.