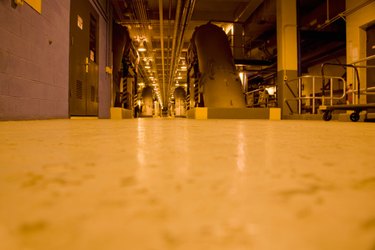
Factory floors need to be highly durable and slip-proof to function well. They cannot react to chemicals, let in moisture or make it any easier for factory accidents to happen. They come under constant and heavy use, especially near loading bays, which means that factory floors can only be made from several different materials that have the necessary protective qualities -- materials often used throughout construction projects.
Concrete
Video of the Day
Concrete is the most basic form of factory flooring. As long as it is stable and perfectly level, it functions well. Concrete can be absorbent, however, so factories typically coat their concrete floors with sealant that prevents any moisture or stain problems. Concrete floors are cost efficient, but they can be damaged through impact.
Video of the Day
Epoxy
Epoxy is a type of chemical resin that cures to form a very hard, durable surface. Floors covered with epoxy are especially good at resisting impact and chemical spills, as well as high temperatures, making them ideal for many factories. Factories need to make the top layer texture to reduce the danger of slipping. Epoxy floors also can be expensive.
Rubber
Rubber floors are relatively easy to install and good at both resisting damage and keeping the floor slip-free. The rubber comes in large rolls that are carefully spread out over the floor and nailed or glued in place. The flooring can be painted more easily than other surfaces, and factories can also choose a sustainable, recycling rubber floor to help promote environmentally responsible activity.
Mezzanine Flooring Options
Mezzanine floors are secondary, raising floors in factories that overlook factory operations. This uses factory space more effectively, and mezzanines are more flexible in terms of flooring options. Wood floors and even carpet can be used on mezzanines, depending on their purpose. Other mezzanines are more suited to concrete or rubber matting.