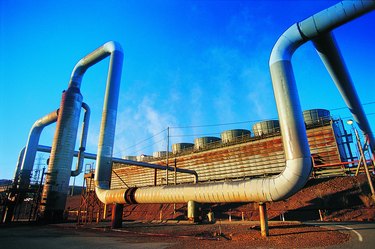
To cast a metal means to shape it by melting it then pouring it into a mold. As the metal cools and solidifies, it adopts the shape of the mold that surrounds it, and once it is completely cool it can be withdrawn. When they want to make cast aluminum products, manufacturers can choose between several methods. One of these is called die casting.
Types
Video of the Day
Casting is a broad term that describes a variety of different methods; die casting is only one of these, although where aluminum is concerned it's one of the three most popular. Two other important approaches are called permanent mold casting and sand casting. While die casting delivers a high level of accuracy and a very consistent shape, sand casting is more versatile and is superior for objects with intricate patterns and designs.
Video of the Day
Die Casting
In die casting, the manufacturer melts the aluminum then forces it into a steel mold at high pressure. The mold is called a die and is made from alloy tool steel divided into two or more sections. One of these sections is called the cover half and remains fixed; the ejector half, by contrast, is removed once the aluminum has solidified, at which point the final product is ejected. The steel mold rapidly conducts heat away from the aluminum so the cooling process is quite rapid.
Sand & Permanent Mold Casting
Sand casting uses a mold made of sand and clay to confine the aluminum while it cools. Sand is a poor conductor of heat, so the cooling process is very slow. The mold is meant to be expendable. In permanent mold casting, by contrast, the mold is made from steel or some other metal and is intended for reuse. The main difference from die casting is that the metal is simply poured into the mold rather than being injected, although sometimes vacuum is applied as well.
Considerations
Each techniques has its advantages. Die casting can be automated and hence is better suited to mass production, although the initial outlay on equipment will typically be greater. Sand casting is more economical for smaller volumes and larger or more complicated products. Permanent mold casting can deliver a stronger and more durable finished product. Many aluminum objects such as car parts or cookware are made through one of these processes, and manufacturers typically choose the approach best suited to the type of object to minimize cost.