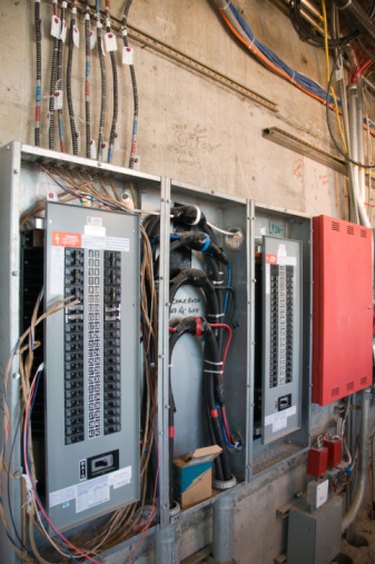
Copper bus connections are critical in any electrical system; improper preparation and connection of bus lugs can cause terminal connections to overheat, creating a fire hazard and contributing to electrical equipment malfunctions. In particular, lug nuts need to be properly torqued to insure a proper electrical and mechanical connection. Torque for bus bar lugs is specified by lug size.
Importance of Torque in Bussing
Video of the Day
A critical concept in understanding bus lug torque specifications is the fact that the pressure of the lug connection has more to do with lowering the resistance of the electrical connection than the size of the lug itself. Loose lugs create a high-resistance connection to the bus bar, and electrical resistance in metal causes heat. The lugs themselves have a greater tendency to heat up than the copper wire itself.
Video of the Day
English Lug Bolts
5/8-11 lug bolts should be torqued to between 55 and 70 foot-pounds. 1/2-13 lug bolts should be torqued between a range of 35 and 50 foot-pounds. 3/9-16 lugs require a torque of between 20 and 30 foot-pounds. 3/9-16 lugs require a torque of between 20 and 30 foot-pounds. 3/9-16 lugs require a torque of between 20 and 30 foot-pounds. Lug bolts sized 1/4-20 should be tensioned to within 5 and 7 foot-pounds.
Metric Lug Bolts
M6 bolts should be torqued to 7.2 Newtons per meter. M8 bolts should be torqued to 17 Newtons per meter. M10 bolts must receive 28 Newtons per meter of torque. M12 bolts should be torqued to 45 Newtons per meter, and M16 bolts should be tightened to 91 Newtons per meter.
Other Considerations
In addition to proper lug tightening, it is important to make sure that the copper bus is flat enough to form a solid contact with the lug. In addition, both bus and lug surfaces must be clean of any oxides or corrosion, which will add resistance to the electrical connection.