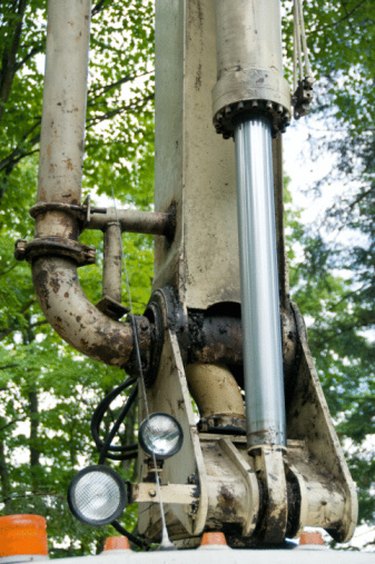
Anodizing aluminum creates aluminum oxide, a strong and durable product used in a variety of construction projects and consumer products. Known for its environmentally safe process and long-lasting, weather-safe finish, anodized aluminum can be customized to level of durability. Hard anodizing refers to an especially strong and durable form of anodized aluminum that differs in thickness and production from standard anodized aluminum.
Types of Anodizing
Video of the Day
There are three general types of anodized aluminum. Chromic anodized -- Type I -- is the thinnest and least corrosive of anodized aluminum. It's produced using chromic acid electrolytes. Sulfuric anodized -- Type II -- and hard anodized -- Type III -- are both produced utilizing sulfuric acid electrolytes. Type II is the most common anodized aluminum and doesn't share the roughened surface of Type III.
Video of the Day
Seal
Standard anodized aluminum is sealed to close pores that occur during the conversion to aluminum oxide. Sealing gives the anodized aluminum a protective coat and prevents color erosion in colored products. Hard anodized aluminum is not generally sealed, as its thicker surface is considered more durable and wear-proof, negating the necessity of a sealant. Waxes and silicone may be used to give hard anodized aluminum a desired finish.
Thickness
Hard anodized aluminum is thicker than standard anodized aluminum. At greater than 25 microns, hard anodized is produced using low temperatures and higher current density to accomplish this thickness. A thicker surface gives hard anodized aluminum a more abrasion-resistant surface.
Uses
Standard sulfuric anodized is employed for architecture, aerospace and automotive components. Products requiring a heavy-duty, wear-resistant surface utilize hard anodized. These include various hydraulics and pistons, some food cooking surfaces and pans, and exterior surfaces of buildings.